6 Methoden zur Optimierung von Carbonfaserverbundwerkstoffen (CFK) mit Hilfe von Tailored Fiber Placement, kurz TFP
von Dr. Christopher Anderson, ZSK Research & Training Center Seattle, WA, USA
Während der Preis für Carbon in den letzten Jahren rapide gesunken ist, bleibt es ein teures und sehr begehrtes Material.
Materialeigenschaften von Carbonfaserverbundwerkstoffen (CFK) wie das Verhältnis von hoher Festigkeit zu Gewicht werden für die folgenden Generation effizienter Transportmittel gesucht. Eine Verringerung des Gewichts eines Fahrzeugs, Flugzeugs oder Raumfahrzeugs kann die kraftstoffeffizienz über die erwartete Lebensdauer erheblich beeinträchtigen. Carbonfaser wird bereits als Ersatz für einige Aluminiumstrukturen genau untersucht, insbesondere aufgrund der damit verbundenen Gewichtsersparnis. Die hohen Materialkosten von Carbonfaserverbundwerkstoffen können jedoch potenzielle Benutzer von den notwendigen Anpassung abhalten.
Darüber hinaus erforderte die Herstellung traditioneller Carbonfaserverbundwerkstoffe mehr Verarbeitungsaufwand als Aluminium. In einem traditionellen Verfahren wurden gewebte Carbonfasergewebe in CAD nachgezeichnet, maßstabsgetreu geschnitten, mit einer Matrix benetzt und in Prozessen wie dem Resin Transfer Moulding (RTM) ausgehärtet. Diese Prozesse sind jedoch oft arbeitsintensiver und es fehlt der Grad der Automatisierung, der bei konkurrierenden Prozessen wie Metallfräsen oder Blechbiegen genutzt werden kann.
Die Technik der maßgeschneiderten Faserplatzierung oder Tailored Fiber Placement kann auf die Herstellung neuer Carbonfaserverbundteile auf material- und prozesseffiziente Weise angewendet werden, um die Kosten erheblich zu senken. Der kurz TFP genannte Prozess ermöglicht die Reduzierung von Carbonfaserabfällen und reduziert so die Materialkosten. Es ermöglicht auch die Kombination anderer Fasermaterialien an ausgewählten Stellen, ermöglicht die Anpassung der Fasern an die spezifische Belastung, ermöglicht eine variable Dicke der Teile und kann problemlos mit neuen Arten technischer Materialien verwendet werden.

Darüber hinaus erfordern Maschinen mit TFP wenig bis gar kein Umrüsten, um von Charge zu Charge sehr unterschiedliche Teile herzustellen, was einen vielseitigeren Herstellungsprozess ermöglicht. Die durch die maßgeschneiderte Faserplatzierung erzielten Optimierungen können dazu beitragen, dass Carbonfaserverbundwerkstoffe zunehmend kostengünstiger werden.
Optimierung 1
Abfall reduzieren
Ein großer, für die hohen Materialkosten verantwortlicher Faktor bei traditionellen Arbeitstechniken ist die große Menge an Verschnitt. Bei vielen manuellen Verarbeitungsprozessen mit Carbonfasergewebe, kann der Verschnitt leicht 50% oder mehr des Gesamtgewichts des verwendeten Carbons ausmachen. Dieser Abfall entsteht, wenn der Stoff vor dem Imprägnieren mit der Matrix zunächst geschnitten wird.
Zusätzlicher Verschnitt und Abfall entsteht, wenn der ausgehärtete Verbundstoff Nachbearbeitet und die Form weiter verfeinert wird.
Tailored Fiber Placement besitzt die einzigartige Fähigkeit, den Verschnitt zu reduzieren und dadurch die hohen Materialkosten bei der Verarbeitungvon Carbon zu senken. Durch präzises Ablegen und fixieren der Carbonfasern in die gewünschte Geometrie wird das Material nur dort platziert, wo es in der endgültigen Preform benötigt wird. Bereiche, die nach der traditionellen Laminattechnik ausgeschnitten werden müssten, bleiben einfach ungestickt. Dieser Prozess reduziert sowohl den anfänglichen Verschnitt, der beim Zuschneiden von Geweben entsteht, als auch den Abfall in der Nachbearbeitung aufgrund der Fähigkeit, komplexe Geometrien legen zu können.
Optimierung 2
Hybrid-Verbundwerkstoffe aus Carbon und Glasfaser
Ein zusätzlicher Nachteil der herkömmlichen Verarbeitung durch Schichten von Carbongewebematten ist der Mangel, das Material so auszutauschen, um von den kombinierten Vorteilen verschiedener Materialien zu profitieren. Tailored Fiber Placement ist eine Methode zur schnellen und effektiven Herstellung dieser Verbundwerkstoffe aus mehreren Materialien.
Wenn beispielsweise eine Strukturanalyse an einem Teil durchgeführt wird, kann festgestellt werden, dass das Teil nur einzelne Bereiche mit lokaler Steifheit benötigt. In diesem Fall können Carbonfasern mit ihrer hohen Steifheit genau an den Bereichen und Geometrien des Teils platziert werden, die diese Steifheit erfordert. Es ist wirtschaftlich unsinnig, das gesamte Teil aus hochsteifen Kohlenstofffasern herzustellen, wenn die hohe Materialfestigkeit nur an bestimmten Stellen erforderlich ist. Um die Kosten weiter zu senken, können daher die Bereiche um die kohlefaserversteifte Geometrie, die keine hohe Steifheit erfordern, mit kostengünstigeren Materialien wie Glasfasern oder sogar Hanffasern gefüllt werden. Durch das Tailored Fiber Placement können diese Materialübergänge nahtlos erfolgen.
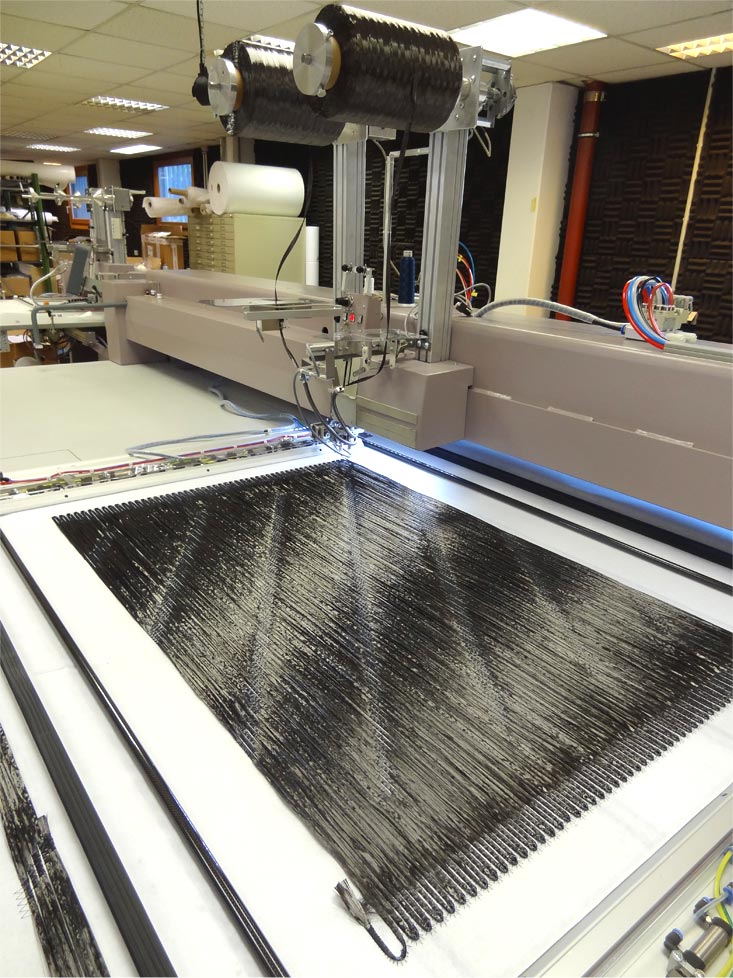
Optimierung 3
Abstimmbare Faserausrichtung und geometrische Anpassungsfähigkeit
Einer der größten Vorteile der Verwendung von Tailored Fiber Placement zur Optimierung eines Designs ist die Möglichkeit, genau zu steuern, wo sich jeder Carbonfaserstrang in einem Design befindet. Auf diese Weise kann der Ingenieur die Materialeigenschaften weiter optimieren und den Bedarf an zusätzlichem Material verringern.
Zum Beispiel können komplexe Strukturen aus Kohlefaser gestickt werden, um die zuvor berechneten Kraftflussverläufen im Bauteil perfekt zu unterstützen. Durch Ausrichten der Fasern auf ihre Hauptspannungen wird eine zusätzliche mechanische Unterstützung bereitgestellt, ohne dass zusätzliches Material verwendet wird. Weitere Optimierungen können durch selektives Verstärken von Löchern und kreisförmigen Bohrpunkten erfolgen. Bei der herkömmlichen Laminatkonstruktion können diese Löcher aufgrund der orthogonalen Natur des verwendeten Gewebes als Bereiche der Rissausbreitung dienen. Tailored Fiber Placement kann verwendet werden, um diese Löcher selektiv mit krummlinigen Mustern zu verstärken, wodurch die effektiven anfänglichen Rissausbreitungsorte verringert werden. Dies kann ein dünneres Material an der Stelle des Lochs und möglicherweise sogar das Entfernen von Metallverstärkungsscheiben ermöglichen.
Optimierung 4
Individualisierbare lokale Materialstärke
Eine weitere interessante Optimierung, die bei der Verwendung einer maßgeschneiderten Faserplatzierung in Kohlefaserverbundwerkstoffen auftreten kann, ist die einstellbare Dicke des Prozesses über einen bestimmten Bereich. Bei der herkömmlichen Laminatkonstruktion wird angenommen, dass Kohlefaserverbundwerkstoffe eine gleichmäßige Dicke aufweisen. Eine maßgeschneiderte Faserplatzierung unterliegt jedoch keiner solchen Höhenbeschränkung. In Kombination mit gut gestalteten Formteilen und Vorrichtungen können Kohlefaser-Vorformlinge eine lokalisierte Dicke in hochkomplizierten und unterschiedlichen Geometrien erzeugen.
In der klassischen Strahlentheorie kann das Trägheitsmoment für einen rechteckigen Strahl berechnet werden durch:
Wenn gezeigt wird, dass die Höhe des Materials (h) einen kubischen Einfluss auf das Trägheitsmoment im Vergleich zur Länge der Basis (b) hat. Dies bedeutet, dass lokalisierte Höhenbereiche mit einer maßgeschneiderten Faserplatzierung erstellt werden können, die wesentlich dazu beitragen kann, Biegungen an dieser Stelle besser zu widerstehen. Diese Optimierung ermöglicht einen verringerten Materialverbrauch, um im Vergleich zu anderen Verbundverfahren die gleichen, wenn nicht sogar verbesserten Schüttguteigenschaften zu erzielen.
ZSK STICKMASCHINEN bietet Maschinen an, die Fasern mit einer Dicke von bis zu 8 mm verlegen können. Dies ergibt durchschnittlich 8 Schichten eines 50 K-Kohlefaserroving. Diese Dicke kann über die gesamte Oberfläche des Preform-Teils gleichmäßig sein oder kann selektiv in wichtigen strukturellen Bereichen platziert werden, um eine zusätzliche mechanische Unterstützung durch das Gewissen des Materials zu gewährleisten.
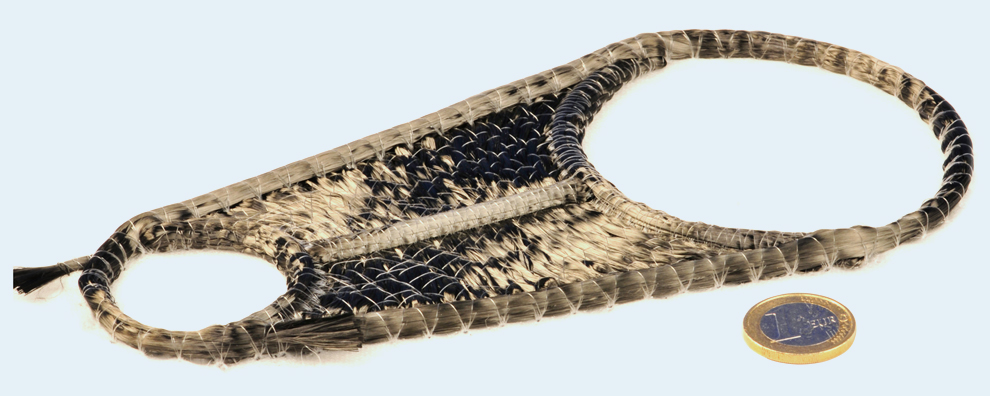
Material wird zur Verstärkung um umfassende Ränder und in der Mitte des Bauteils zusätzlich aufgebracht.
Diese lokale Materialverdickungen ermöglichen es dem Bauteil, Biegemomente statisch besser aufzunehmen.
Gleichzeitig werden durch die berechneten lokalen Verstärkungen die Materialkosten gesenkt, indem Bereiche, die statisch nicht so beansprucht werden, kostengünstig mit einfacher Materialstärke auskommen.
Diese zusammengesetzten Materialien können auf die gleiche Weise wie andere maßgeschneiderte Verbundmaterialien für die Faserplatzierung genäht werden. Diese Vorformlinge können jedoch in beheizten Pressen schnell thermocyclisiert werden, um die Zyklusverarbeitungszeit schnell zu verkürzen. Herkömmliche duroplastische Verbundwerkstoffe, die Harztransferformen verwenden, können zwischen 30 Minuten und 40 Stunden benötigen, um ein einzelnes Stück richtig abzusetzen und auszuhärten.
Die maßgeschneiderte Faserplatzierung von Commingled Yarn ermöglicht die Platzierung sowohl der Verstärkungsfaser als auch der thermoplastischen Fasern in derselben Vorform. Beim Erhitzen der Preform wird die flüssige Matrix direkt in der Kohlefaser verteilt, was eine ordnungsgemäße Benetzung ermöglicht. Die maßgeschneiderte Faserplatzierung von Comeled-Fasern macht zusätzliche Harze überflüssig und kann die Materialkosten erheblich senken. Zusätzlich wird während des Comeling-Schritts die gewünschte Faser-Volumen-Fraktion erzeugt, wodurch die Gleichmäßigkeit des Verbundmaterials von Charge zu Charge erhöht wird.
Schließlich sind diese Verbundfaserverbundwerkstoffe ein Schritt in Richtung eines nachhaltigeren Kohlefaserverbundwerkstoffs, da sie am Ende ihres Lebenszyklus wieder in neue Formen geschmolzen werden können.
Optimierung 6
Vielseitigkeit der Maschine ohne Umrüsten
Eine weitere wichtige Prozessoptimierung, die bei einer maßgeschneiderten Faserplatzierung im Vergleich zu anderen Verbundprozessen auftritt, ist die Fähigkeit der Produktionsmaschine, ihre Produktion ohne zusätzliche Umrüstung der Maschine schnell von einem Design auf ein völlig anderes Design umzustellen. Auf diese Weise kann dieselbe Maschine nahtlos von der Herstellung von Autoteilen in der Morgenschicht auf Sportgeräte in der Nachmittagsschicht umgestellt werden.
Darüber hinaus kann eine maßgeschneiderte Faserplatzierung es derselben Maschine ermöglichen, jeweils einen Prototyp zu erstellen, um einen Prozess zu untersuchen und Fehler zu beheben, ohne überschüssiges Material zu verschwenden, und gleichzeitig einen vollständigen Produktionslauf zu erstellen. Dieses schnelle Prototyping für die Produktionsfähigkeit in Kombination mit der Fähigkeit einer Maschine, viele verschiedene Arten und Geometrien von Teilen in schneller Folge auszuführen, ermöglicht es, vielseitigere Projekte auf derselben Maschine auszuführen. Dies reduziert die Kosten für die Einrichtung einer neuen Maschine jedes Mal, wenn ein neues Design generiert wird.
Zusammenfassend zeigen die sechs kurz vorgestellten Optimierungsmethoden für Kohlefaserverbundwerkstoffe einige der Vorteile einer maßgeschneiderten Faserplatzierung gegenüber herkömmlichen Verbundwerkstoffverfahren. Es ist zu hoffen, dass die Kombination dieser Optimierungsmethoden in Verbindung mit dem Trend, die Kosten für Kohlefasermaterialien zu senken, eine neue Klasse allgegenwärtiger und hochentwickelter Materialien ermöglicht, um Anwendungsfälle für Verbraucher wie die Kraftstoffeffizienz weiter zu verbessern.
ZSK bietet Maschinen für die maßgeschneiderte Faserplatzierung (TFP) für eine Vielzahl von Teilegrößen und Basisszenarien an. Prototyping-Maschinen sind mit 1 Kopf erhältlich, um schnell neue Prototypen mit minimaler Rüstzeit oder Materialaufwand herzustellen, während Produktionsmaschinen mit bis zu 11 Köpfen erhältlich sind, die gleichzeitig Fasern für die Massenproduktion verlegen können. Die nutzbare Maschinenfeldfläche für eine 8-Kopf-Maschine beträgt 900 mm x 1.900 mm pro Kopf. Dies bedeutet, dass das Teil, solange es in den Bereich von 900 mm x 1.900 mm passt, 8 Mal gleichzeitig pro Lauf erstellt und dupliziert werden kann. Für größere Teile, die nicht in diesen Bereich passen, kann eine 8-Kopf-Maschine innerhalb weniger Minuten im laufenden Betrieb zu einer 4-Kopf-Maschine umgebaut werden. Dies ermöglicht eine maximale Teilegröße von 1.800 mm mal 1.900 mm. Es gibt andere anpassbare Lösungen, einschließlich Rolle-zu-Rolle- und Spezialplatzierungsmaschinen für noch größere Teile.