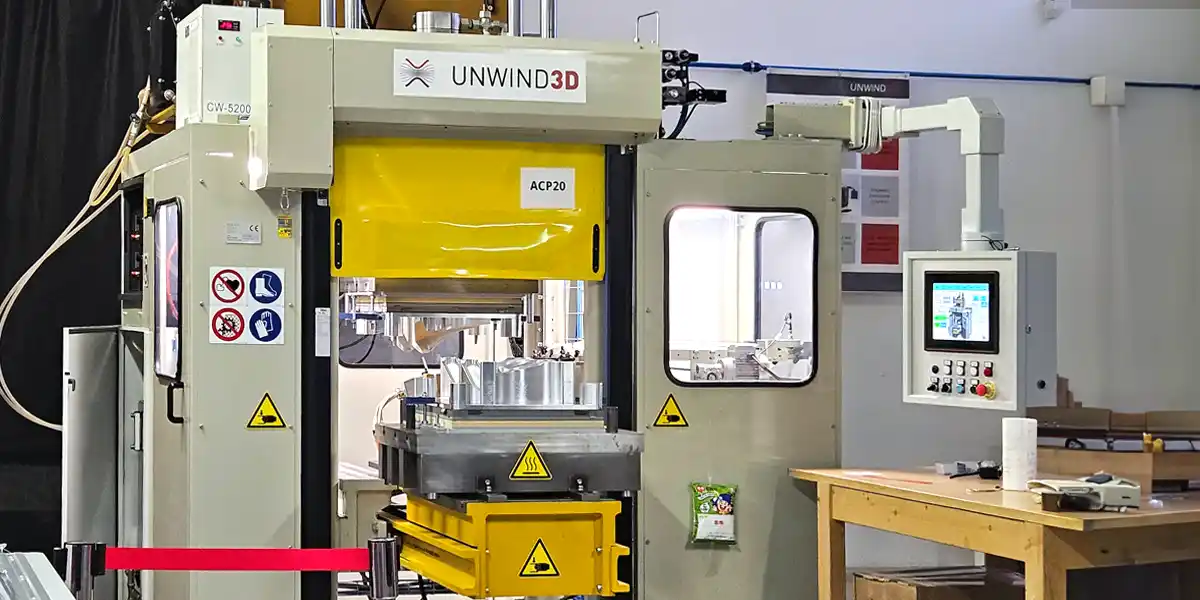
Thermoplastische Verbundbauteile präzise gefertigt mit TFP-Technologie
Von der 2D-Preform zum 3D-Bauteil – nahtlos, reproduzierbar und wirtschaftlich
UNWIND3D ist ein spezialisiertes Technologieunternehmen im Bereich Faserverbundtechnik. Mit umfassender Expertise formt UNWIND3D netzförmige, mehrlagige TFP-Preforms zu hochpräzisen 3D-Verbundbauteilen – für thermoplastische und duroplastische Matrixsysteme.
Ob rein TFP-basierte Strukturen oder hybride Layups – UNWIND3D schließt die Lücke zwischen Faserablage und Fertigteil. Vom Prototyp bis zur Serienproduktion unterstützt das Team aus dem Innovationszentrum in Italien Industriepartner bei der Umsetzung effizienter Composite-Lösungen.
Formgebung für Thermoplaste – gezielt gelöst
Während klassische Preforms beim Aufschmelzen des Matrixmaterials an Volumen verlieren, setzt UNWIND3D auf speziell entwickelte Umformprozesse. So lassen sich Herausforderungen wie Druckverteilung, Temperaturführung und Werkzeugkonstruktion präzise beherrschen.
Mit fundiertem Prozesswissen und maßgeschneiderter Anlagentechnik ermöglicht UNWIND3D die industrielle Herstellung von Thermoplast-Verbundbauteilen in mittleren Stückzahlen – bei exzellenter Maßhaltigkeit und struktureller Qualität.
Die eingesetzte Technologie hat ihre industrielle Leistungsfähigkeit bereits bewiesen – mit einem durchgängigen Betrieb von 9 Stunden täglich über einen Zeitraum von 10 Monaten in der Kundenproduktion.
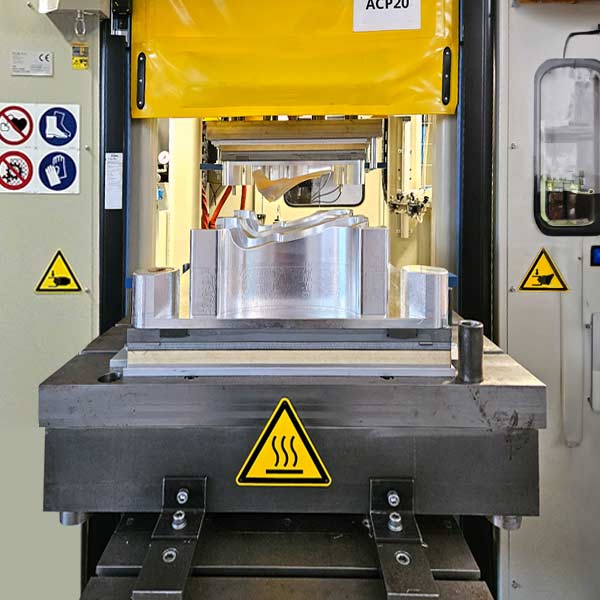
Vorsprung durch Technologie – die Stärken von UNWIND3D
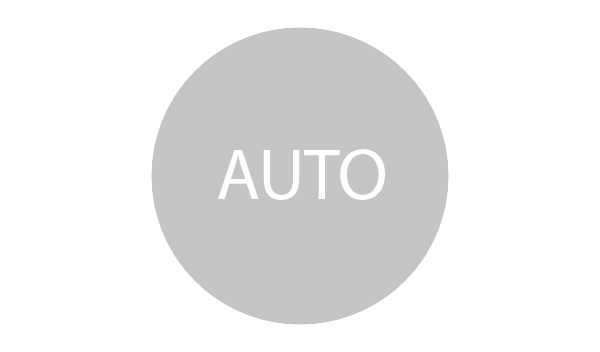
Automatisierte Produktion mit maximaler Wiederholgenauigkeit
Ideal für Serienfertigung: reduziert Personalaufwand, steigert Prozesssicherheit und garantiert gleichbleibende Bauteilqualität.
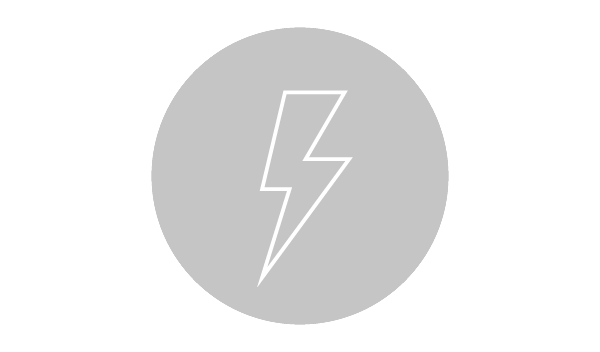
Effizient im Verbrauch – stark in der Leistung
Intelligentes Energie- und Druckmanagement senkt Betriebskosten ohne Abstriche bei Durchsatz und Qualität.
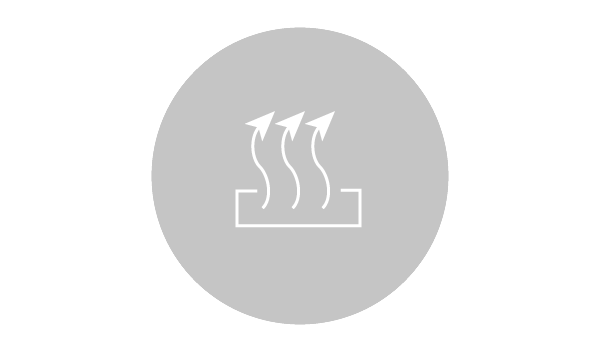
Zwei Heizsysteme – ein Ziel: kurze Taktzeiten
Induktions- und Konduktionswärme sorgen für schnelle, gleichmäßige Erwärmung – ideal für Thermoplaste und Duroplaste.
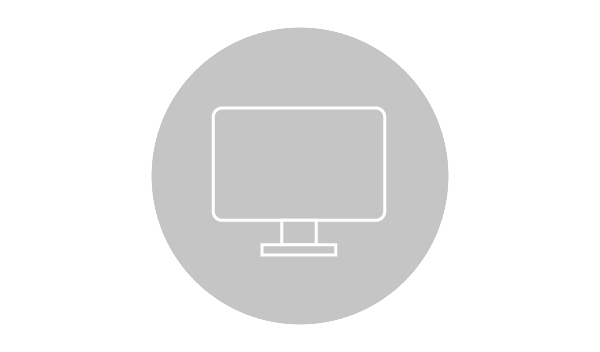
Intuitive Prozesssteuerung – individuell anpassbar
Die eigenentwickelte Steuerungssoftware bietet einfache Bedienung, präzise Parametrierung und energetische Optimierung.
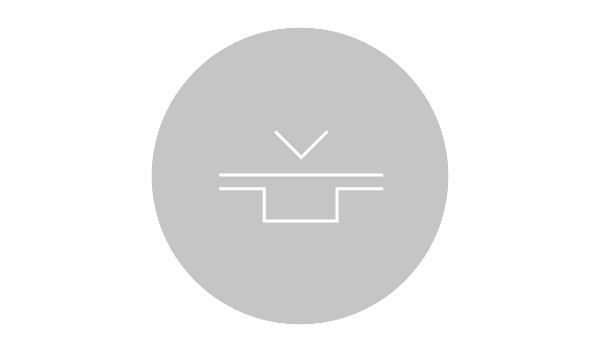
Druck, der sich anpasst – für bessere Ergebnisse
Dynamische Druckregelung reduziert Lufteinschlüsse, erhöht die Integrität der Bauteile und verlängert die Lebensdauer der Werkzeuge.
Anwendungsbeispiel: Carbonfaser-Verstärkung im Reitsattel
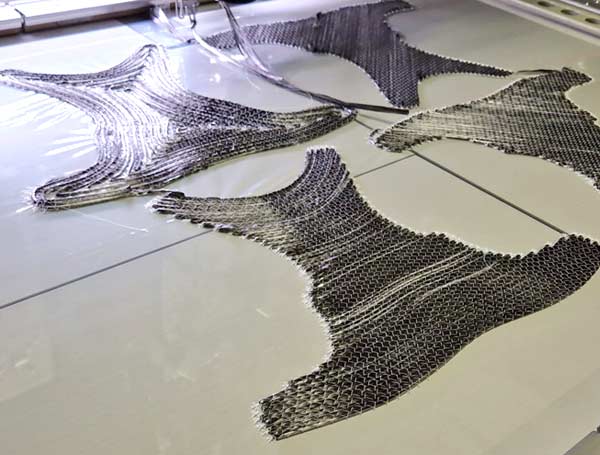
Automatisierte TFP-Preform-Fertigung
Fasergenau ausgelegt mit der Tailored-Fiber-Placement-Technologie von ZSK.
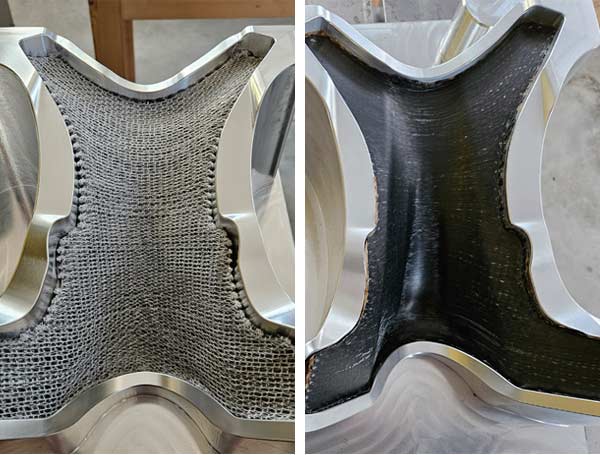
Nahtlos geformt – passgenau gefügt
Netzförmige Preform vor und nach der Formgebung – thermoplastisch konsolidiert.
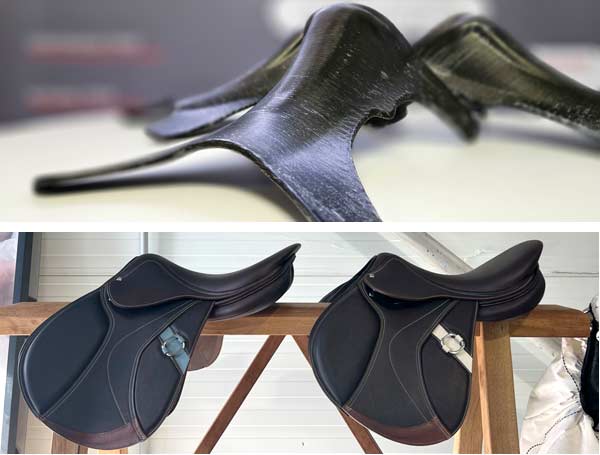
Montage und Endprodukt
Das geformte Carbonfaser-Bauteil verstärkt die tragende Struktur eines Reitsattels – leicht, steif und formgenau.
In dieser Anwendung entstehen über 1.000 Bauteile pro Monat im Einschichtbetrieb – ein Beispiel für die industrielle Leistungsfähigkeit und Prozesssicherheit von UNWIND3D.