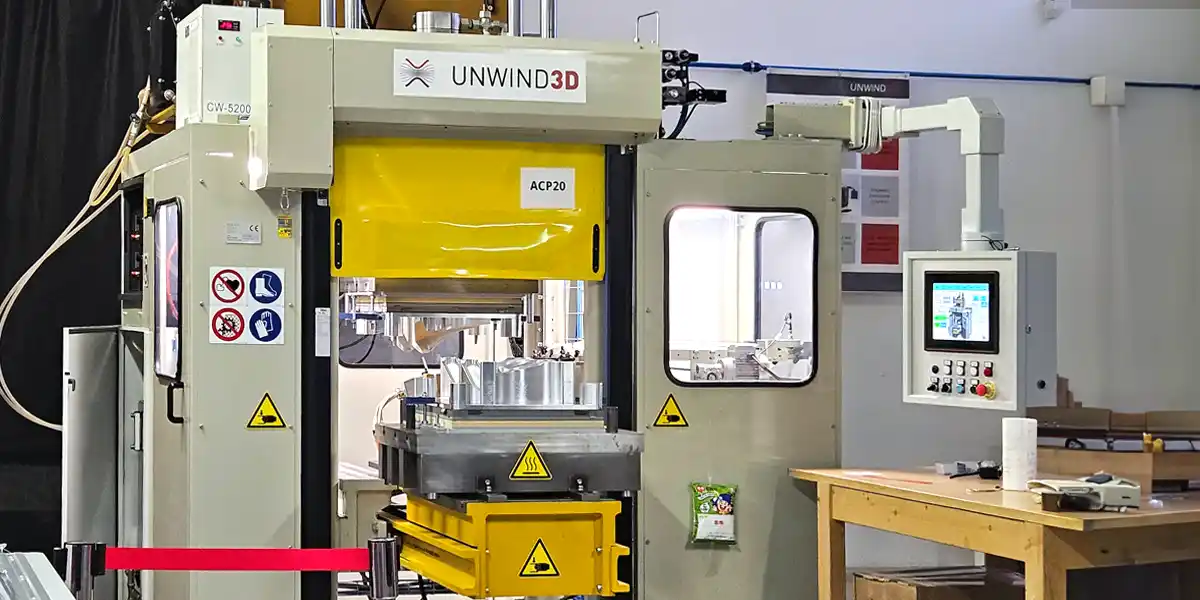
Precision Manufacturing of Thermoplastic Composites with TFP Technology
From 2D Preform to 3D Component – Seamless, Repeatable and Efficient
UNWIND3D is a specialised composite technology company with deep expertise in shaping net-shape, multilayer TFP preforms into high-precision 3D composite parts – using both thermoplastic and thermoset matrix systems.
Whether producing fully TFP-based structures or hybrid layups, UNWIND3D bridges the gap between fibre placement and final part. From prototype to series production, the team at the Italian innovation centre supports industrial partners in implementing efficient composite solutions.
Thermoplastic Forming – Challenges Solved by Design
Where conventional preforms tend to shrink as the matrix melts, UNWIND3D relies on purpose-built forming processes. This ensures precise control of pressure, temperature distribution and tool design – even with complex geometries and demanding matrices.
With in-house process expertise and tailored equipment, UNWIND3D enables the reliable production of thermoplastic composite parts in medium volumes – with excellent dimensional stability and structural performance.
The technology has already proven itself in industrial environments – with continuous operation of 9 hours per day over a period of 10 months at customer production sites.
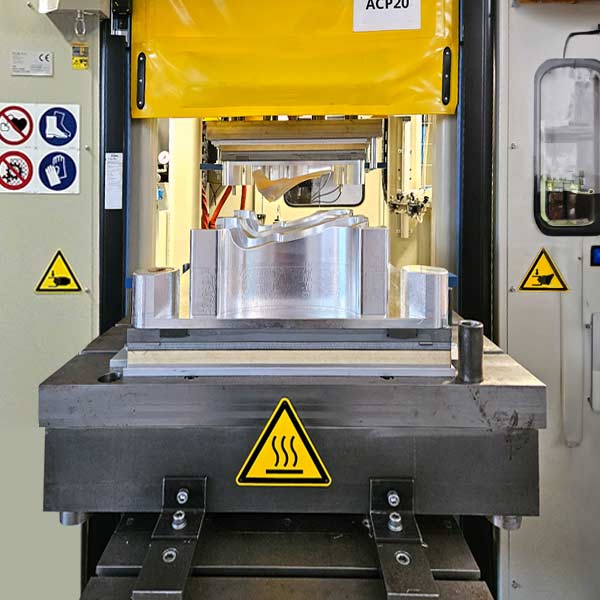
Technology That Makes the Difference – UNWIND3D Advantages
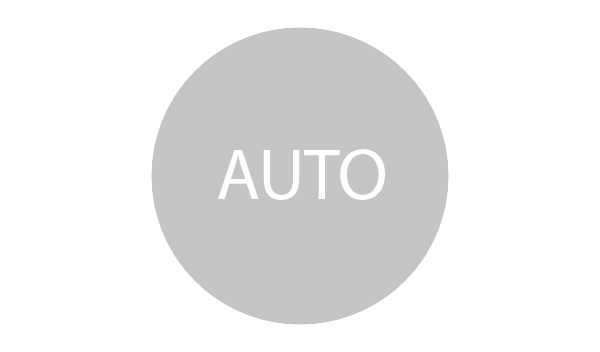
Automated Production with Maximum Repeatability
Ideal for series production: reduces labour costs, increases process reliability and guarantees consistent part quality.
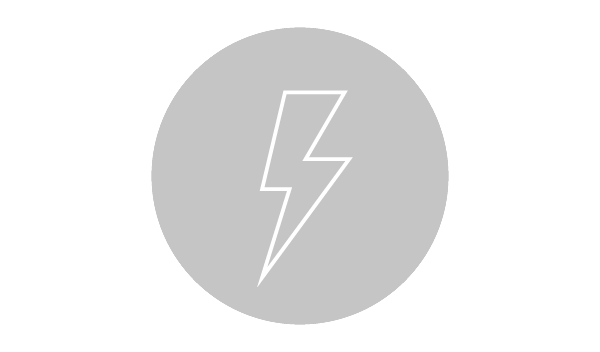
Efficient by Design – Powerful in Performance
Smart pressure and energy management reduces operating costs without compromising throughput or quality.
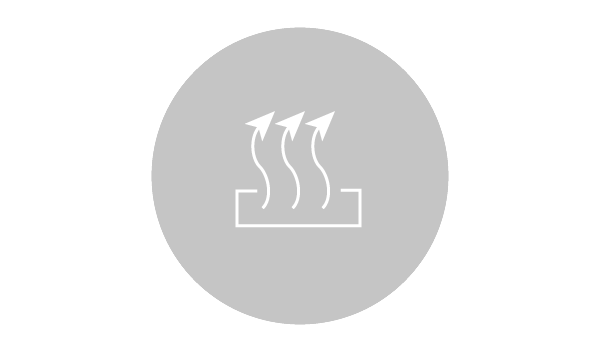
Two Heating Systems – One Goal: Shorter Cycles
Induction and conduction heating ensure fast, even heat transfer – ideal for thermoplastics and thermosets.
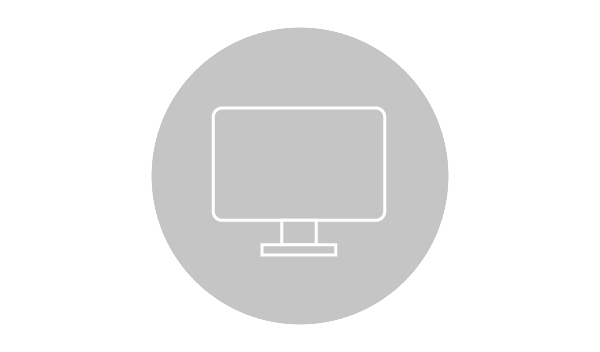
Intuitive Process Control – Built for Adaptability
The proprietary control software offers user-friendly operation, precise parameter control and efficient energy management.
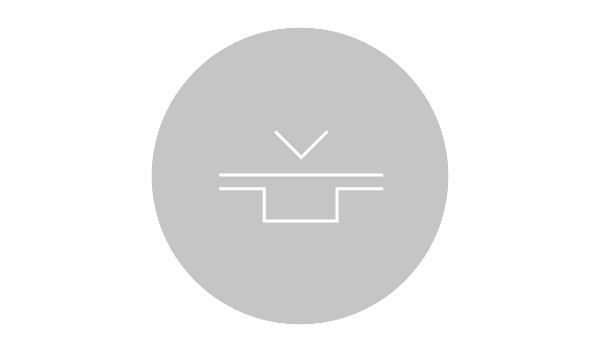
Adaptive Pressure – For Better Results
Dynamic pressure regulation improves part integrity, reduces voids and extends tool life – while lowering energy consumption.
Case Study: Carbon Fibre Reinforcement in Equestrian Saddles
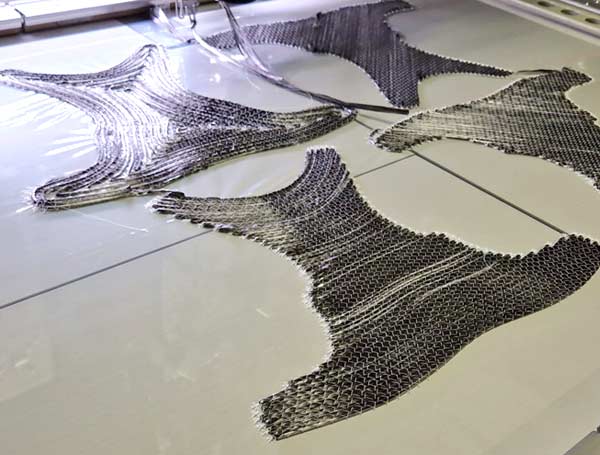
Automated TFP Preform Manufacturing
Fibre-precise layup using Tailored Fibre Placement technology from ZSK.
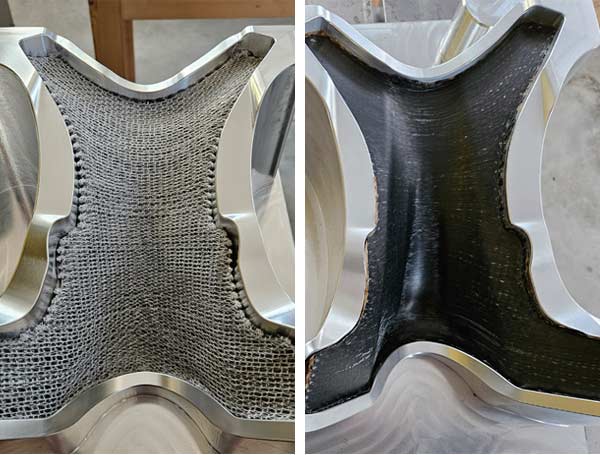
Seamlessly Formed – Precisely Consolidated
Net-shape preform shown before and after the forming process – thermoplastically consolidated.
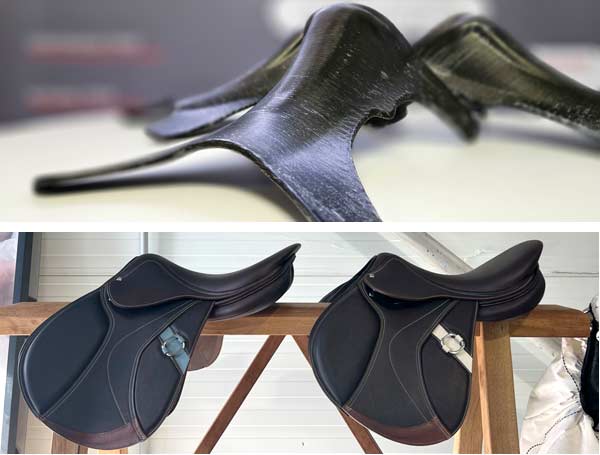
Final Assembly
The moulded carbon fibre component reinforces the saddle’s structural core – lightweight, stiff and dimensionally accurate.
In this application, more than 1,000 parts are produced each month in a single-shift operation – demonstrating UNWIND3D’s industrial performance and process reliability.