Weltweit erster „bestickter“ Composite-Fahrradsattel mit ShapeTex ™ Technologie
Das Fahrrad ist mittlerweile erste Wahl bei den umweltfreundlichen Transportmitteln. In den letzten 10 Jahren hat die Branche neben der technologischen Entwicklung verschiedener Aspekte des Push-Bike-Designs ein beispielloses Wachstum verzeichnet, von hochmodernen Aero-Rahmen bis hin zu leichten Komponenten wie Lenker, Räder und Sättel, um nur einige zu nennen.
Im Oktober 2017 begannen zwei Maschinenbaustudenten an der School of Engineering and Computing der Oxford Brookes University mit Design- und Forschungsarbeiten im Bereich Fahrradsättel. Die industrielle Zusammenarbeit mit Shape Machining Ltd. mit Sitz in Witney hat zur Entwicklung eines leichten Fahrradsattels über sieben Monate geführt, bei dem das ShapeTex ™ -Komposit-Herstellungsverfahren verwendet wird, bei dem Mischgarne aus Kohlenstoff und Nylon auf eine Nylonfolie gestickt werden, um ein Netz herzustellen. geformter Vorformling, der dann in weniger als 5 Minuten gepresst werden kann.
In der Anfangsphase der Entwicklung wurden einige Untersuchungen zu Aspekten der Sattelform durchgeführt, die Komfort bieten, beispielsweise die Aufnahme eines zentralen Ausschnitts, der zur Verringerung der perinealen Kompression beiträgt. Studien zu den Auswirkungen verschiedener Schalengeometrien auf die Stabilität wurden ebenfalls berücksichtigt. Vier verschiedene Preform-Designs wurden in der ANSYS FEA-Software unter Verwendung von Composite-Modellierungswerkzeugen modelliert.
Diese Phase half dabei, einen Einblick in eine optimale Form und Faserorientierung zu erhalten, um die Schalenfestigkeit zu maximieren und das Laminatdesign zu beeinflussen. Im Rahmen des Modellierungsprozesses wurden einige der mechanischen Eigenschaften experimentell durch einfache Zugversuche an unidirektionalen Kohlefaserprüfkörpern bestimmt, die nach dem ShapeTex ™ -Verfahren hergestellt wurden.
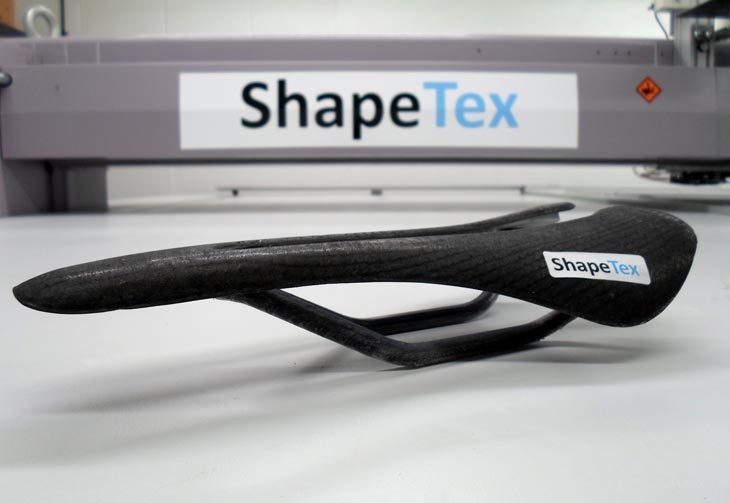
Parallel dazu wurde von den Studenten unter umfassender Anleitung des erfahrenen SHAPE-Ingenieurteams ein umfassender zweiteiliger Entwurfsprozess für Presswerkzeuge durchgeführt. Dieser Prozess war aufgrund einiger komplexer geometrischer Merkmale der Sattelform wie gekrümmte Oberflächen, zentraler Ausschnitt usw. mit einigen Herausforderungen verbunden. Die Metallformen wurden von einem anderen Projektpartner, Borga Cycles in der Nähe von Mailand, aus einer Aluminium-Billet-Legierung CNC-gefräst Italien. Die hohen Härtungstemperaturen für die Vorformlinge wurden im Rahmen des Konstruktionsprozesses berücksichtigt.
Um die visuelle Ästhetik zu fördern und einen gleichmäßigen Oberflächenkontakt in der Form bereitzustellen, wurde eine Vliesstoffmischung aus recycelten kurzen Kohlenstoff- und Nylonfasern auf den 2D-Vorformling aufgenäht. Der fertige Vorformling wurde in die Form gegeben und hohen Drücken und Temperaturen ausgesetzt.
Die Verwendung eines MarkForge 2-Verbund-3D-Druckers wurde zur Herstellung von Verbundfilamentsattelschienen verwendet. In diesem Fall erwies sich dies als kostengünstiger und weniger komplex im Gegensatz zur Herstellung von Formen. Eine Kombination aus einer geeigneten kontinuierlichen Füllung mit kontinuierlichem Kohlefaseranteil und einer optimalen Faserorientierung innerhalb der Schienen lieferte die erforderliche Steifheit und Festigkeit. Die bedruckten Schienen wurden mit Acrylkleber 3M DP8405 auf die Schale geklebt. Zuvor wurde eine Reihe von Überlappungsschertests unter Verwendung des oben genannten Acrylklebstoffs durchgeführt, um seine Festigkeit zu bewerten.
Schließlich wurde der geklebte Prototypsattel für einige Vorversuche an einer Fahrradsattelstütze befestigt. Vier verschiedene Radfahrer fuhren mit dem Fahrrad und die Sattelstruktur blieb untrennbar. Obwohl der Umfang der Tests sehr begrenzt war, zeigte sie das Potenzial der Verwendung einer solchen Fertigungstechnologie für tragende Anwendungen.
Zusammenfassend hat sich das Fahrradsattelprojekt als hervorragendes Beispiel erwiesen, das das Potenzial der akademischen und industriellen Zusammenarbeit zur weiteren Erforschung der ShapeTex-Fertigungstechnologie und zur Herstellung maßgeschneiderter Verbundvorformlinge für bestimmte Anwendungen demonstriert.
Weltweit erster „bestickter“ Composite-Fahrradsattel mit ShapeTex ™ Technologie
Über SHAPE
SHAPE Machining
ist spezialisiert auf die Bearbeitung von Metallwerkzeugen, Epoxid-Werkzeugblockmustern, Rohacell-Schäumen und das Trimmen von Kohlefaserteilen für die Automobil-, Motorsport- und Luftfahrtindustrie.
SHAPE Engineering
bietet eine umfassende Palette von Design-, Analyse- und Projektmanagement-Services zur Unterstützung von Projekten zur Herstellung von Verbundteilen und Werkzeugen.
SHAPE Composites
liefert duroplastische und thermoplastische Verbundvorformlinge und Teile, die von maßgeschneiderten autoklavengehärteten Kohlenstoffteilen bis zu größeren Mengen heißgepresster geformter Kohlenstoffteile reichen.
ShapeTex
Optimiertes Design und Herstellung von Kohlefaser-Preforms.
Kontakt
Wenden Sie sich an info@shape-group.com, um weitere Informationen zu erhalten.
Online: www.shape-group.com