A major difference between a sewing machine and an embroidery machine is the capability to have a variety of colours (needles) per head. ZSK offers embroidery machines with 6, 9, 12, 18 and 24 needles. In general, one can say that a higher number of needles leads to reduced downtimes for changing of threads on the machine. Customers choose to have a higher number of needles to have more colours on the machine, to have a variety of thread types (i.e. very thin thread for sharp and crisp lettering and normal embroidery thread) or they choose a low number of needles in favour of space between the heads. Especially towel embroidery houses typically tend to have a low number of needles to roll up the towels in-between the heads. Certain ZSK models such as the 56 head machine are limited to 6 needles due to their head spacing.
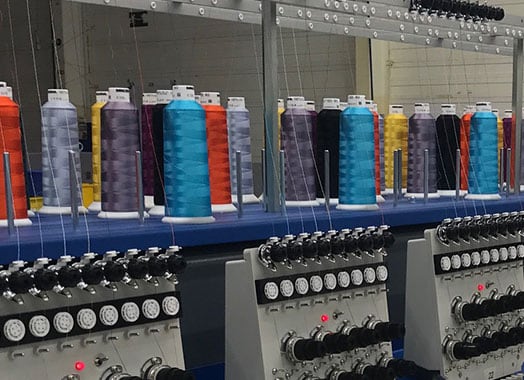
Each color change costs time
The Right Strategy – the downtime in-between colour changes can be optimized with the right strategy. If a certain design is expected to be produced in a large volume, it makes sense to place the required thread cones next to each other, so that the path for the colour change motor is the shortest and quickest possible.
In larger production environments with often changing designs, colours are often placed at random on the machines. Many customers tend to block a certain number of needles for standard colours (white, black, red, blue, etc.). These colours are on the first needles and are never exchanged as they are used in the majority of designs.
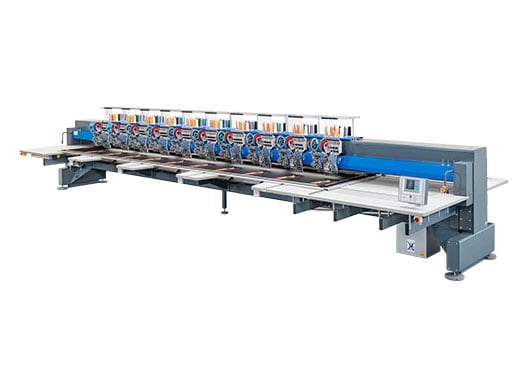
Fast color change
Customers using devices on their machines (sequins, cording) have to constantly move the heads between needle 1 and i.e. 12. The time this process takes is a downtime. Therefore, designs should be digitized in a way, so that these changes occur as little as possible. In some cases these cannot be avoided. In 2018 ZSK introduced the Fast Colour Change in the Challenger and Racer II Series to offer a solution that reduces these downtimes heavily.
Optional feature
The Fast Colour Change is an optional feature for the Challenger Series and certain Racer machines and a standard feature on all Racer II Series machines. The time for colour changes (12 needles) is reduced to below 2 seconds. In combination with the new catcher motor customers have found efficiency increases of up to 10%. Such increases depend on the complexity of designs, but especially those embroidery houses that handle a lot of small batches benefit greatly from this development.
CHALLENGER series
Designed for efficient production in borders or single frames, the range of machines ranges from 10 to 15 heads with 9 or 12 needles, which are controlled and driven by the new control electronics MCP 35, latest absolute encoders and powerful servomotors.
RACER series
With the embroidery machines of the new series RACER, we set again the world standard for tubular embroidery machines. Developed and manufactured in Germany, this machine concept guarantees the shortest return of investment thanks to the highest embroidery speed.

RACER
State of the art technology – With the embroidery machines of the new series RACER, we set again the world standard for tubular embroidery machines.
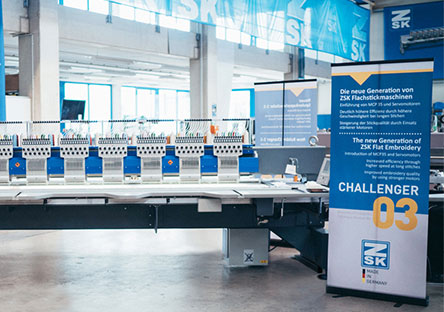
CHALLENGER
Our flat bed embroidery machines are the ideal means of production with which you can meet even the highest quality requirements of your customers.