The key to success using Tailored Fiber Placement
by Matteo Moretti, Project Manager ZSK TECHNICAL EMBROIDERY SYSTEMS
This article aims to be a guide towards highlighting the advantages in using TFP Technology, explaining when and how this technology should be considered to fully replace standard manufacturing, or how the technology could be integrated to existing processes.
In the recent years, the growth of Technical Embroidery Systems has been exponential. Technical Embroidery Machines developed by ZSK are now well established and largely used into the automotive, aerospace, sport and leisure industries. Among the wide range of technical embroidery technologies (i.e. Tailored Wire Placement, Smart Textiles, E-Textiles, Functional Sequins), Tailored Fibre Placement (TFP) is particularly experiencing the greatest interest and demand in the composite industry.
Arranging and stitching a fibre tow on a compatible backing material exactly where reinforcement is most needed for structural performance, TFP embroidery machines allow the user to create nearly net-shape preforms that serve a unique role in the manufacturing process. By implementing net-shape preforms, composites parts are increasingly becoming more cost competitive, while waste material is reduced and the structure is highly optimized.
How and when should one implement this technology for composites manufacturing parts? What materials should be used? This knowledge is the key to success and innovation for most of ZSK’s technical customers.
TFP using Thermoplastic Commingled Fibre Yarns
Commingled yarns consist in a mixture of thermoplastic and reinforcement fibre. While the latest reinforcement fibres are usually carbon or fibre glass, the thermoplastic fibre could be Nylon (PA6), Polypropylene (PP), Thermoplastic Polyurethane (TPU) or Polyetheretherketone (PEEK).
The type of thermoplastic to use is mainly chosen depending on the structural requirements of the final product application. For the same reason, the desired fibre to volume fraction could be varied during the commingling process, increasing the uniformity of the composite material from batch to batch.
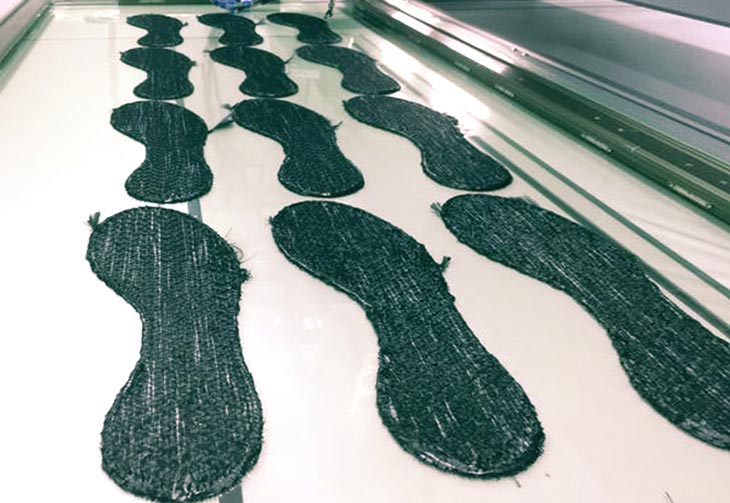
Fig.1: A batch of commingled thermoplastic preforms.
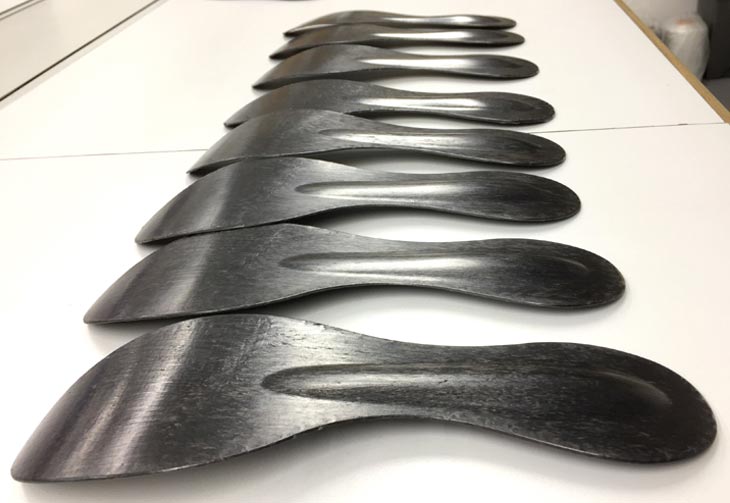
Fig. 2: The moulded preforms, after a compression moulding cycle of under 3 minutes.
Preforms constructed using commingled yarns, do not require any extra resin to be injected in the moulding process; the thermoplastic fibre, which normally matches the thermoplastic backing material, will melt and act as the bonding matrix in the composite structure.
This results to speed up and automate drastically the entire composite manufacturing process; appositely designed and shape-optimized TFP preforms are simply placed into the moulds and therefore consolidated into the finished parts through heating and cooling stages as part of the compression moulding cycle for thermoplastic materials.
Post-processes simplicity is strictly dictated by the part’s geometry and the mould’s design; more complex parts would eventually require the edges to be CNC-trimmed; flatter components instead (such as composite inner shoe sole shown in Fig.1 & 2), would be net-shaped consolidated in closed moulds, manually and quickly deburring the edges.
The sport and leisure industries are demonstrating enthusiastic interest in implementing TFP technology using thermoplastic commingled yarns, which allows companies to bring on the markets innovative, lighter and performant products at a competitive price. Finally, the resulting products tend to be more sustainable due to their ability to be re-melted into new forms at the end of their lifecycle.
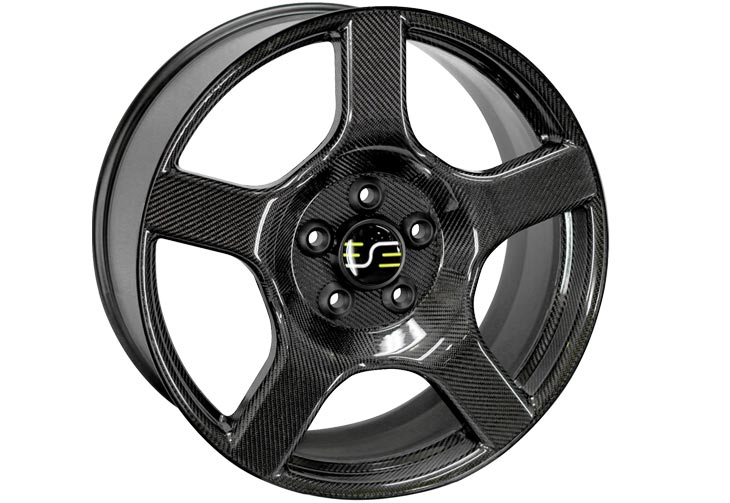
Fig. 3: The E2’s five spokes Wheel
TFP using ‘Pure’ Fibre Yarns
Preforms constructed made out using Pure Fibre yarns (i.e. carbon, glass, aramid glass fibre, aramid fibre) should be thought as reinforcements for the final composite product, to be appositely integrated within the existing manufacturing process such as Resin Transfer Moulding (RTM) or Resin Infusion Moulding (RIM).
A great example is represented by E2’s Five Spokes Carbon Fibre Wheel, developed by ESE Carbon in USA. Carlos Hermida, CEO at ESE Carbon, in one of his most recent interviews stated that „the technology has allowed the company to reduce ply consumption by up to 50%, thereby creating a simplified layup process and minimizing waste. Carbon fibre waste was reduced from around 40% with traditional carbon fibre fabrics to less than 10% by adopting TFP. In addition, the technology has led to improved layup quality, optimized fibre orientation, and increased design flexibility“.
Figure 3 shows respectively ‘the wheel reinforcement preform’ created by using ZSK Technical Embrodery Systems TFP technical machine, and the final moulded ESE’s Five Spokes Carbon Fibre Wheel.
The same use and application case of the technology is widely adopted by many of major ZSK STICKMASCHINEN customers in the automotive and aerospace industries.
Nevertheless, if the lower productivity rate has been the main concern when using TFP technology, ZSK Technical Embroidery Systems has now brought its TFP technical machines to the next level through a number of patented innovations that speed up the deposition of fibre, making the technology even more suitable for larger reinforcement preforms.
Less than a year ago, ZSK STICKMASCHINEN has launched the HV-TFP technology.
The principle is rather simple, where two rovings are laid down simultaneously, each being stitched with a linear density more than two times faster than in the actual process. This new functionality, combined with Fast Fibre Laying, allow the manufacturer to increase the productivity of the machine, thus increasing the benefit and applicable use of TFP even for large structural parts.
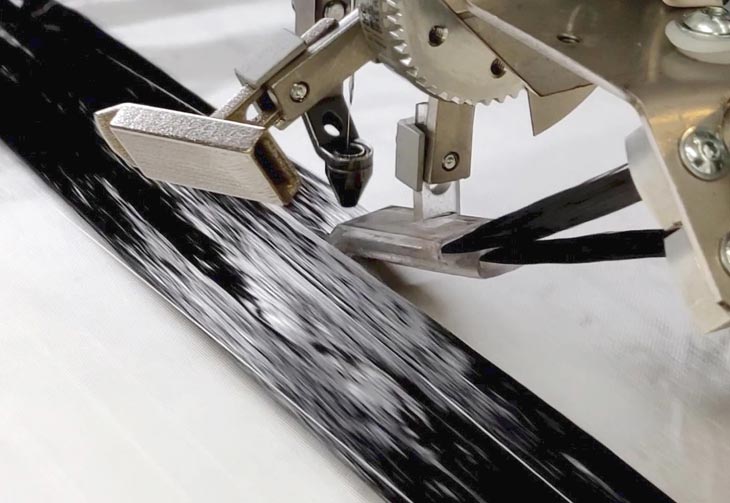
Fig. 4: Fast Fibre Laying + HV-TFP on ZSK Technical Embroidery Systems
To summarize, depending on product’s dimensions, materials, and structural requirements, TFP provides a valuable resource to the composites design and manufacturing community. If considering thermoset based composite parts, TFP then should be seen as a ‘plus’ when compared to the existing manufacturing processes, and suitable for the production of small to large reinforcement parts.
On the other hand, when it comes to thermoplastic-based composite parts, TFP could be considered to fully replace standard manufacturing processes for the production of small to medium size composite products. In either case, even though production is completed in different scales and in different industries, the evident benefits brought by TFP technology supported by ZSK Stickmaschinen‘s technical innovations are the reason of its considerable and constant growth in the recent years.