Success with tradition and Innovation
Albrecht Bender in Weißenburg was founded in 1864 in Ansbach. In 1892, the company was acquired by the grandfather of the current managing director, as the company was registered and approved as a supplier to ancient royal Bavarian regiments. Today, the family-owned business is run by the third generation, Gerhard Fürst, with the support of his son Roland Fürst and factory manager Ludwig Pfaller.
Albrecht Bender is a specialized manufacturer of all kinds of uniform accessories – from emblems to laces and trimmings. With its extensive range of high-quality products of steady quality, Bender supplies the retail market, industry, government agencies and public organizations. Among their main customers are armed forces, fire brigades, police forces, railway services as well as international airlines and organizations like NATO, THE UNITED NATIONS and even European Royal Dynasties. Apart from its headquarters in Weißenburg, the company has branches in Czech Republic and Tunisia where machine embroidery is predominant. On a small scale, hand-embroidery is still being offered. The group employs a total of 350 international employees.
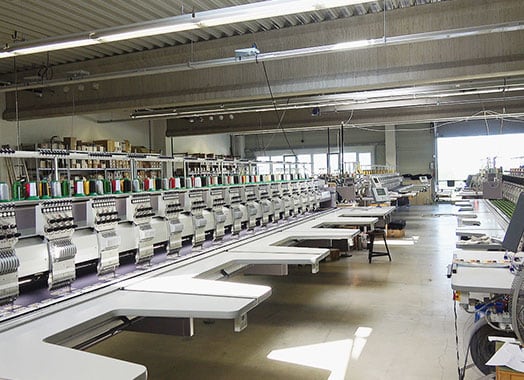
Embroidery department
Since the very early days, Albrecht Bender has been offering items that are refined and individualized with artistic hand-embroidery. Already back in 1933, Albrecht Bender had its first embroidery machine in use. Over the past decades, the machine embroidery business has grown considerably, and the equipment has been adapted to the expanding business.
"Those days in Atlanta"
Until 1996, embroidery on ribbons and tapes was done with embroidery frames on so-called name stripe machines. In the long term and with the growing quantities, this system was no longer up-to-date and no longer efficient. The process of laying carrier material into the frame was too time-consuming. Consequently, in 1996 Mr. Fürst was looking for a solution that could automatically pull and transport woven ribbons and tapes, while embroidering the carrier material. He had samples stitched at all well-known international embroidery machine manufacturers. The result however was not satisfactory. Some patterns were imprecise, some were precise, but with an embroidery look that was totally inappropriate for the European market. The ideal solution was not there yet. At the trade fair in Atlanta in 1996, Mr. Fürst first met with the ZSK management and with Mr. Metzler, at that time head of the ZSK software department. Shortly after this conversation, the idea was born and the solution found.
Within the following weeks, ZSK engineers developed equipment according to the customer’s requirements. And just after six month the first five ZSK embroidery machines with the new developed technology were delivered to Bender. At least as revolutionary as the ribbon equipment was a software developed by ZSK, the ZSK “Production Manager”. Albrecht Bender used this software already in 1996 for the central administration of their monograms and was probably one of the first companies at that time with a fully automated workflow for personalized name embroidery.
The Albrecht Bender machine embroidery department is one of the most advanced in the world. Today, the company has almost 100 of the latest computerized ZSK embroidery machines from the SPRINT, RACER and CHALLENGER series, starting from single-head up to 18-head machines. The numerous single-head machines equipped with Roll2Basket are mainly used for the production of name stripes. The four 18-head machines, Mr. Fürst’s so-called “battleships”, are particularly used for the mass production of badges.
Digital and computerized in the past and today
Next to the embroidery hall is the process planning department where we see how Bender employees “communicate” with the embroidery machines in their factory. As already described, individual name embroidery is a fully automated work process here since long. Process planners are sending orders exclusively from the server to the individual embroidery machines. The ZSK “Production Manager” is the software providing the central competence for these processes.
Advantages in day-to-day business
The advantage of a network is that all patterns are stored centrally on the server. The setup time at the embroidery machine is reduced, errors in the name transfer are eliminated. Given the multitude of names, this is a huge advantage for the company and a relief for the employees. In the event of capacity bottlenecks, jobs can be easily and quickly transferred to any free machine available on the network. Small machines can be managed without large personnel and embroiderers can handle the big machines instead.
Challenge and USP
It is not an easy task to successfully organize, structure and manage all of this. Thanks to the experienced and prudent management and a committed team with a headcount of 350 employees, and state-of-the-art machinery including 450 high-performance and smart ZSK embroidery