Multiple Materials - Single Process
Have you ever thought about merging shape and function in one seamless process?
Integrate fibers like carbon or glass fiber with wires in a single production step!
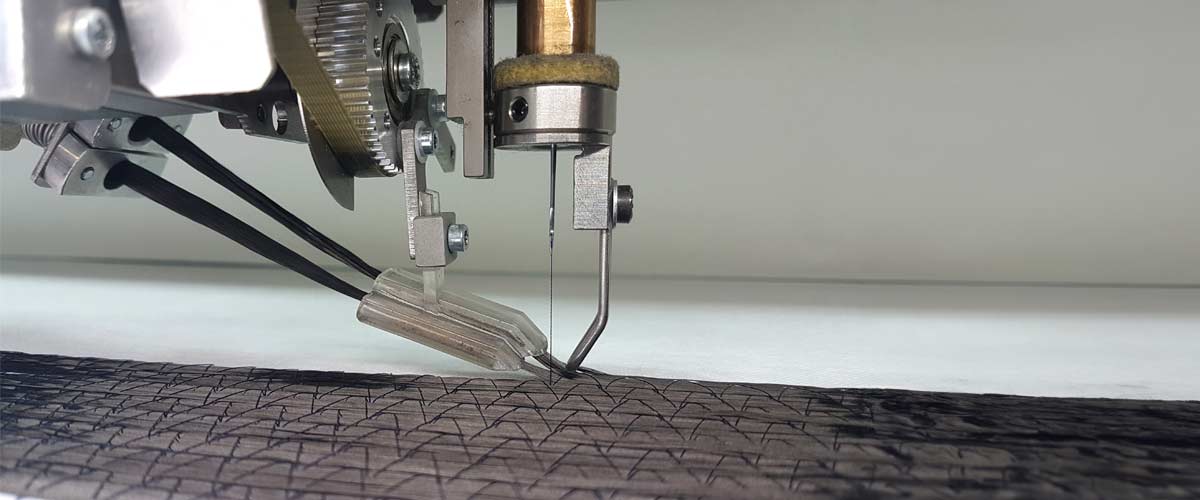
ADVANCED COMPOSITE SOLUTIONS FOR UAVs

Tailored Fiber Placement (TFP) is an advanced additive manufacturing process that enables automated lay-up with reinforcement fibers placed exactly where needed.
This load-path optimized, net-shape preforming method reduces waste while enhancing structural performance. ZSK TFP technology is highly scalable and flexible, allowing for radial, concentric, and localized reinforcement, seamlessly integrating into traditional composites manufacturing methods such as: RTM, injection molding, compression molding, resin infusion, etc.
UAV & DRONE COMPOSITE MANUFACTURING
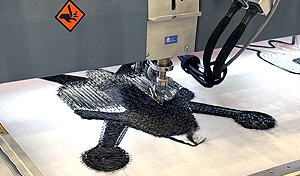
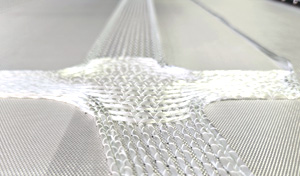
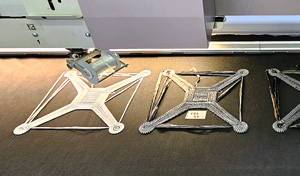
TFP revolutionizes UAV and drone production by enabling automated fiber lay up with precise and optimized reinforcement, achieving lighter yet stronger structures.
Unlike traditional composite layups, TFP allows curved fiber paths, optimizing load distribution and impact resistance.
With ZSK’s automated TFP technology, manufacturers can produce high-performance, net-shape drone components with minimal waste, enhanced durability, and maximum efficiency.
FUNCTIONAL INTEGRATION WITH TAILORED WIRE PLACEMENT (TWP)
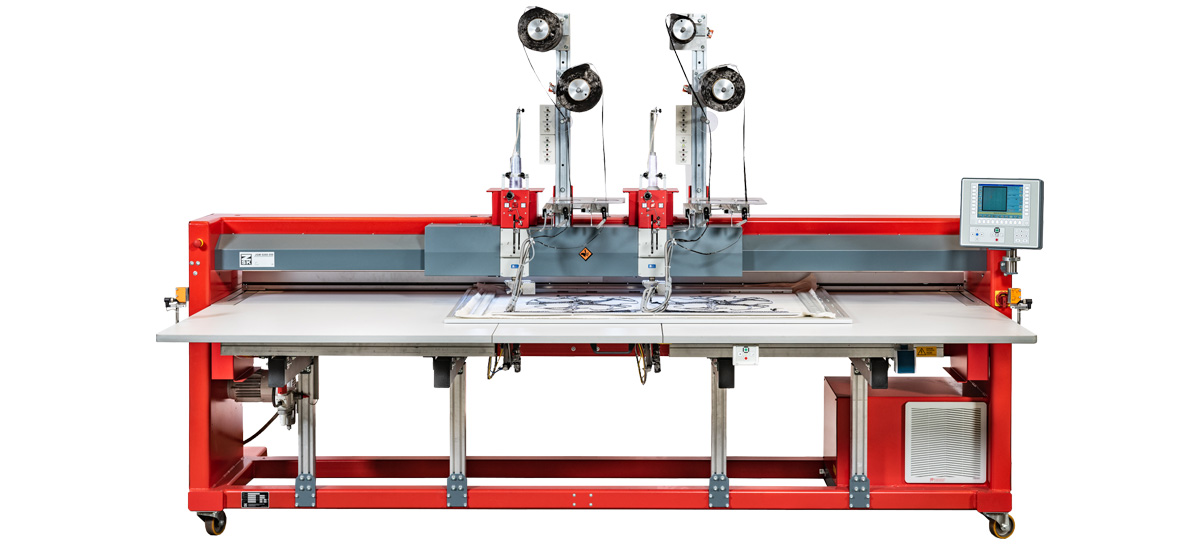
Tailored Wire Placement (TWP) expands composite capabilities by embedding cables, tubes, and optical fibers into the structure, enabling heating, cooling, data, and power transfer. When combined with TFP, functional composites can be created, embedding sensors, antennas, and power systems inside the component itself.
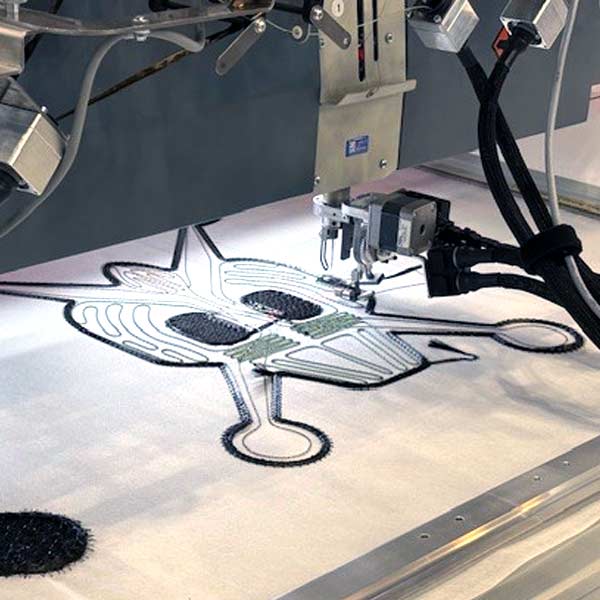
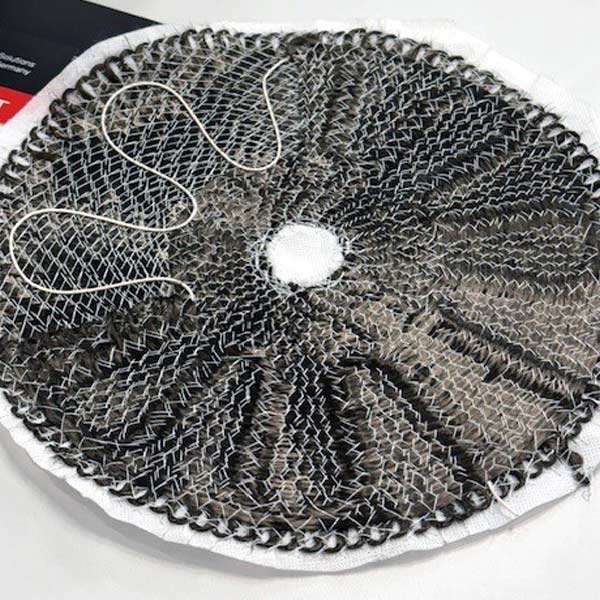
ONE SHOT UAV FRAME PRODUCTION
WITH ZSK AUTOMATED MATERIAL SWITCHING
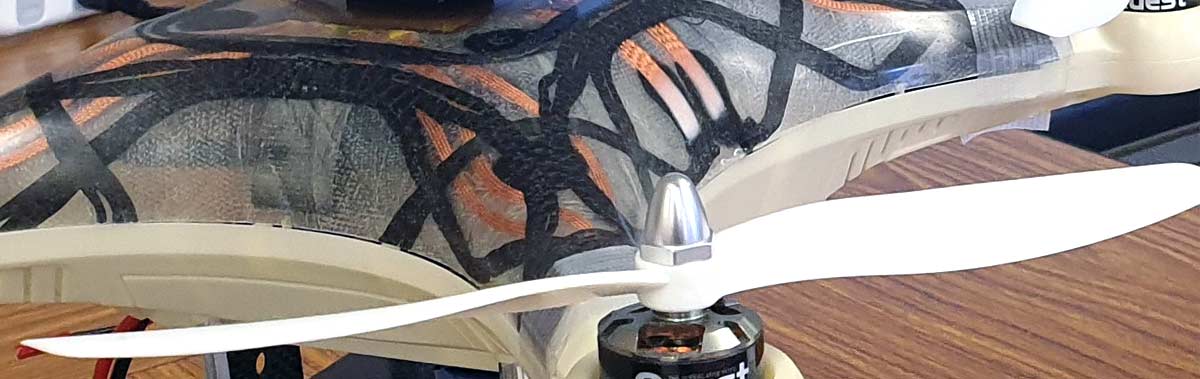
ZSK’s automated material switching allows seamless integration of TFP and TWP via triple-material integration, demonstrated in the production of a functional composites drone frame. The process automatically switches between:
- Carbon fiber reinforcement for structural rigidity
- Antenna cable for communication
- Power cable for motor operation
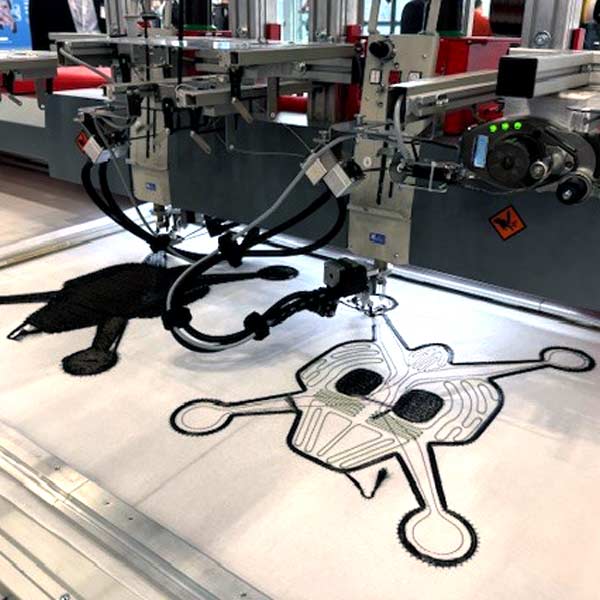
The 2 preforms will be moulded together and were made separately to ensure full customization of the composite frame and of the wire path.This could also be done in a one shot process on a ZSK machine allowing to embed functionality directly within the structure.
Alternativ ist dieser Vorgang auch als One-Shot-Prozess auf einer ZSK Maschine realisierbar – Struktur und Funktion in einem einzigen Ablauf.
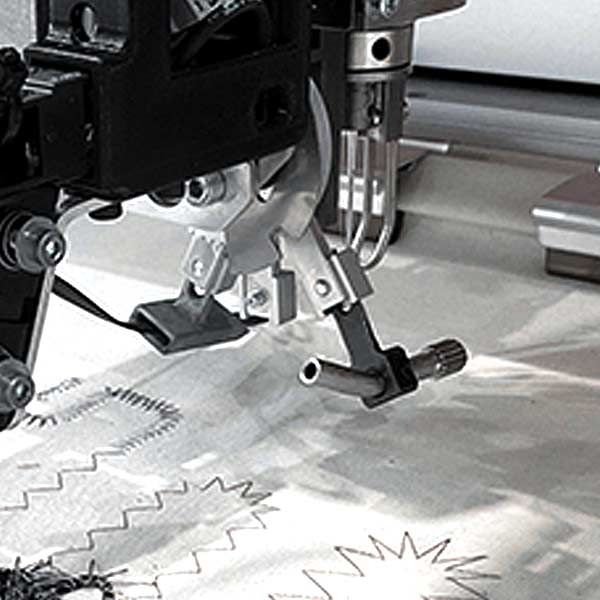
The same automated switching system can also be applied to
- TWP applications – Laying down three different cables in a single process
- TFP applications – Combining two reinforcement fibers with a matrix fiber for optimized mechanical properties