Enhance Your Composites with TFP Technology
In the race for lighter, stronger, and more intelligent composite components, conventional production methods often reach their limits. That’s why NOBRAK, a French pioneer in sustainable composites, chose ZSK’s TFP technology – enabling precise fibre layouts with zero compromise.
One of our valued customers, NOBRAK, is achieving great success with TFP machines from ZSK. Founded eight years ago in Montauban, this French SME specialises in high-tech, bio-inspired composite design with complex fibre architecture.
With a team of ten experts in textiles, composites, and advanced manufacturing, NOBRAK combines craftsmanship with cutting-edge innovation. Their tailored solutions support demanding industries such as automotive, aerospace, and sports – all relying on ZSK technology to meet high industrial and environmental standards.
THE CHALLENGE
Why conventional methods fall short.
→ Limited flexibility, control, and material efficiency.
While traditional methods such as fabric layups or prepregs are established, they restrict fibre orientation to standard angles like [0°], [45°], or [90°]. Composite manufacturing requires greater flexibility to maximise performance and streamline production.
THE SOLUTION
How ZSK’s TFP system delivers.
→ Accurate fibre placement, design freedom, and repeatability.
ZSK’s TFP systems enable highly precise fibre placement. The technology is defined by five core advantages:
- Total customisation
Fibres are laid exactly where needed, tailored to meet specific performance requirements. - Functional integration
Mechanical inserts, sensors, RFID chips and more can be embedded into textile preforms using HV-TFP. - Improved durability
Reduced waste and optimised material use extend product life and resource efficiency. - Lightweight and strong
Components that are both light and structurally rigid – ideal for high-performance sectors like aerospace, automotive, and sports. - Versatile application
Suited for sandwich panels, complex geometries, or integrated inserts – perfect for advanced assembly solutions.
THE COLLABORATION
Joint development, training, and integration.
→ Hands-on support from ZSK, driven by shared innovation.
ZSK and NOBRAK work in close partnership.
NOBRAK’s patented HV-TFP (High Volume Tailored Fibre Placement) technology is fully compatible with ZSK machines. It is one of the few systems capable of simultaneously addressing the technical, economic, and ecological demands of modern composite manufacturing.
High Volume TFP
Together with NOBRAK, ZSK developed a patented process for parallel fibre placement – doubling throughput and increasing production efficiency for serial manufacturing.
Fast Fibre Laying
The patented system enables high-speed fibre placement without stitching. Up to eight angular layers can be laid in sequence, with the final layer secured by continuous stitching.
Combined Performance
The combination of High Volume TFP and Fast Fibre Laying increases productivity to up to 1,980 g/h (24K) – a major advance over conventional TFP methods.
THE IMPACT
Results, product output, and performance gains.
→ Lighter, stronger, and more efficient composite structures.
TFP and HV-TFP are reshaping the limits of composite manufacturing – enabling lighter builds with enhanced structural performance and efficiency.
THE FUTURE
Outlook on future projects and innovation.
→ Expanding TFP applications, entering new markets, and driving R&D forward.
NOBRAK is committed to expanding the use of TFP across the composite industry. Serving clients worldwide, they supply parts to the automotive, aerospace, sports and leisure sectors. To support broader adoption, accurate modelling and optimisation of composite structures – particularly for urban mobility – are at the heart of ongoing research and development activities.
HIGHLIGHT
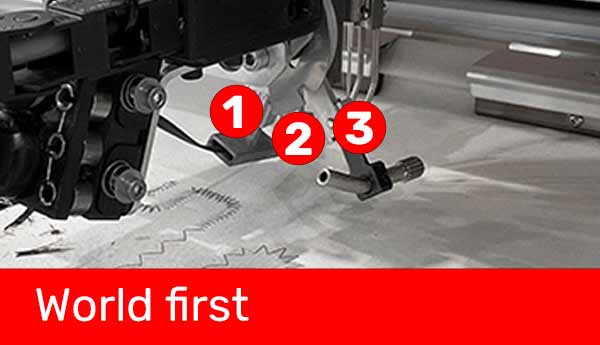
ZSK’s automated material switching system enables seamless integration of TFP and TWP using triple-material guidance.
Example: A functional composite drone frame.
The process automatically switches between:
- Carbon fibre reinforcement for structural rigidity
- Antenna cable for communication.